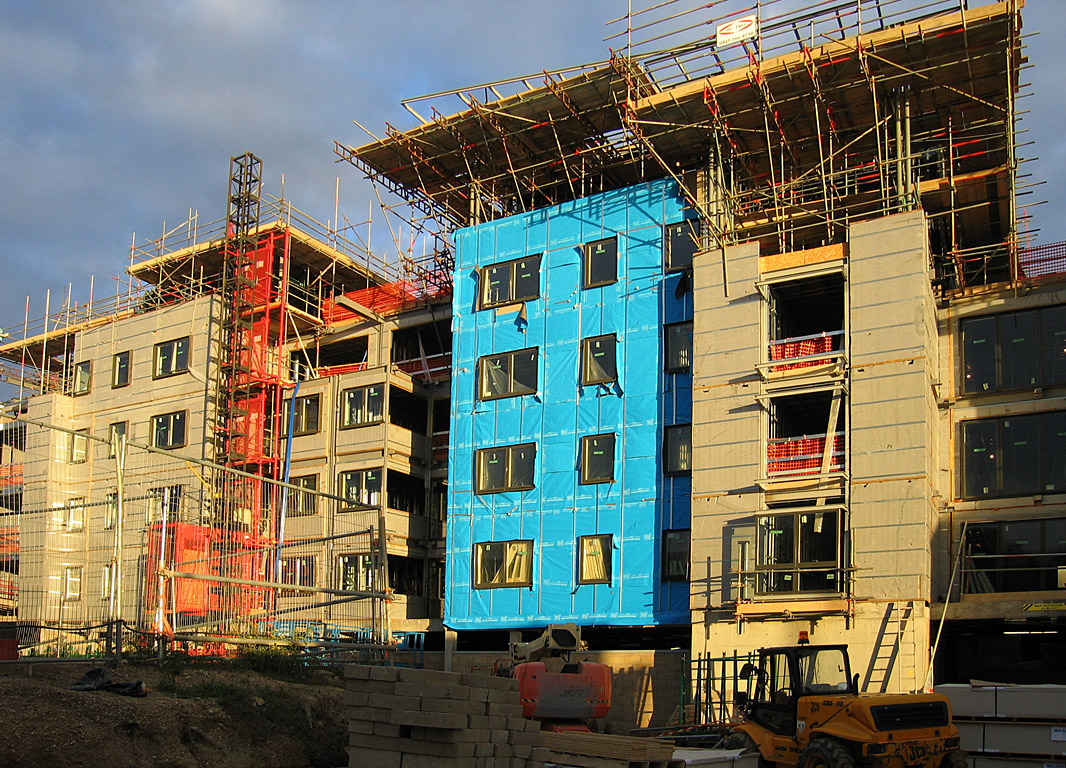
Building insulation material
Building insulation materials are the building materials that form the thermal envelope of a building or otherwise reduce heat transfer.
Insulation may be categorized by its composition (natural or synthetic materials), form (batts, blankets, loose-fill, spray foam, and panels), structural contribution (insulating concrete forms, structured panels, and straw bales), functional mode (conductive, radiative, convective), resistance to heat transfer, environmental impacts, and more. Sometimes a thermally reflective surface called a radiant barrier is added to a material to reduce the transfer of heat through radiation as well as conduction. The choice of which material or combination of materials is used depends on a wide variety of factors. Some insulation materials have health risks, some so significant the materials are no longer allowed to be used but remain in use in some older buildings such as asbestos fibers and urea.
Factors affecting the type and amount of insulation to use in a building include:
Considerations regarding building and climate:
Often a combination of materials is used to achieve an optimum solution and there are products which combine different types of insulation into a single form.
Health and safety issues[edit]
Spray polyurethane foam (SPF)[edit]
All polyurethane foams are composed of petrochemicals. Foam insulation often uses hazardous chemicals with high human toxicity, such as isocyanates, benzene and toluene. The foaming agents no longer use ozone-depleting substances. Personal Protective Equipment is required for all people in the area being sprayed to eliminate exposure to isocyanates which constitute about 50% of the foam raw material.[2]
Fiberglass[edit]
Fiberglass is the most common residential insulating material, and is usually applied as batts of insulation, pressed between studs. Health and safety issues include potential cancer risk from exposure to glass fibers, formaldehyde off-gassing from the backing/resin, use of petrochemicals in the resin, and the environmental health aspects of the production process. Green building practices shun Fiberglass insulation.
The World Health Organization has declared fiber glass insulation as potentially carcinogenic (WHO, 1998[34]). In October 2001, an international expert review by the International Agency for Research on Cancer (IARC) re-evaluated the 1988 IARC assessment of glass fibers and removed glass wools from its list of possible carcinogens by downgrading the classification of these fibers from Group 2B (possible carcinogen) to Group 3 (not classifiable as to carcinogenicity in humans). All fiber glass wools that are commonly used for thermal and acoustical insulation are included in this classification. IARC noted specifically: "Epidemiologic studies published during the 15 years since the previous IARC Monographs review of these fibers in 1988 provide no evidence of increased risks of lung cancer or mesothelioma (cancer of the lining of the body cavities) from occupational exposures during manufacture of these materials, and inadequate evidence overall of any cancer risk."
The IARC downgrade is consistent with the conclusion reached by the US National Academy of Sciences, which in 2000 found "no significant association between fiber exposure and lung cancer or nonmalignant respiratory disease in the MVF [man-made vitreous fiber] manufacturing environment." However, manufacturers continue to provide cancer risk warning labels on their products, apparently as indeminfication against claims.
However, the literature should be considered carefully before determining that the risks should be disregarded. The OSHA chemical sampling page provides a summary of the risks, as does the NIOSH Pocket Guide.
Miraflex is a new type of fiberglass batt that has curly fibers that are less itchy and create less dust. You can also look for fiberglass products factory-wrapped in plastic or fabric.
Fiberglass is energy intensive in manufacture. Fiberglass fibers are bound into batts using adhesive binders, which can contain adhesives that can slowly release formaldehyde over many years.[35] The industry is mitigating this issue by switching to binder materials not containing formaldehyde; some manufacturers offer agriculturally based binder resins made from soybean oil. Formaldehyde-free batts and batts made with varying amounts of recycled glass (some approaching 50% post-consumer recycled content) are available.